Diecasting has become an essential component of Malaysia’s manufacturing landscape, playing a crucial role in the nation’s industrial development and economic growth. This intricate process, which involves forcing molten metal into molds to create precise and complex shapes, is fundamental in producing high-quality metal components used across various industries. Over the years, Malaysia’s diecasting industry has evolved significantly, driven by technological advancements, skilled labor, and strategic government policies. This evolution reflects the broader aspirations of Malaysia to position itself as a key player in the global manufacturing arena, supplying high-quality diecast parts to sectors such as automotive, electronics, and consumer goods.
The origins of diecasting in Malaysia date back to the mid-20th century, aligning with the country’s early industrialization efforts. Initially, diecasting was primarily used for producing simple metal parts for local consumption. However, as Malaysia’s economy diversified and industrialized, the demand for more sophisticated and high-precision diecast components surged. This demand was especially pronounced in the automotive and electronics sectors, which require reliable and high-quality parts for their products. Recognizing the potential of diecasting to drive industrial productivity, the Malaysian government implemented policies to support the industry’s development, including investments in infrastructure and technology, thereby creating a conducive environment for growth and innovation.
Technological advancements have been instrumental in the growth and sophistication of Malaysia’s diecasting industry. The adoption of computer-aided design (CAD) and computer-aided manufacturing (CAM) technologies has revolutionized the diecasting process, enabling greater precision, efficiency, and complexity in part design and production. Modern techniques such as vacuum diecasting and squeeze casting have further enhanced the quality and durability of diecast parts. Additionally, innovations in materials science have led to the development of new alloys with superior properties, expanding the range of applications for diecast components. These technological improvements have enabled Malaysian diecasters to meet stringent international quality standards, making them competitive players on the global stage.
The automotive industry is a major beneficiary of Malaysia’s advanced diecasting capabilities. Diecast components are integral to manufacturing various automotive parts, including engine blocks, transmission cases, and structural components. The precision and reliability of diecast parts make them ideal for the automotive sector, where performance and durability are paramount. Malaysia’s strategic location and robust infrastructure have attracted numerous global automotive manufacturers, further boosting the demand for diecast components. Consequently, Malaysia has emerged as a critical player in the global automotive supply chain, leveraging its diecasting expertise to support industry growth and meet the evolving needs of automotive manufacturers worldwide.
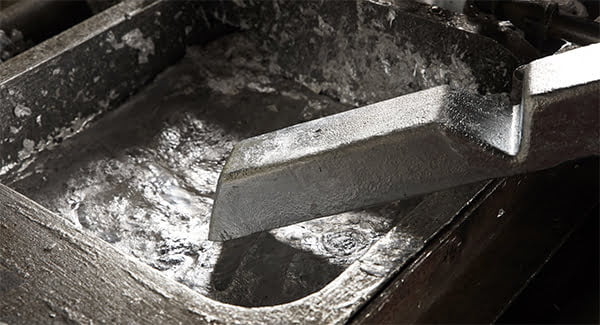
In addition to the automotive sector, the electronics industry also relies heavily on diecasting for producing intricate and precise components. Diecasting is used to manufacture parts such as electronic housings, connectors, and heat sinks. The rapidly growing consumer electronics market, driven by increasing demand for devices like smartphones, tablets, and laptops, has created significant opportunities for precision machining malaysia. By maintaining high-quality production standards and leveraging advanced manufacturing technologies, Malaysia has positioned itself as a reliable supplier of diecast components to the global electronics industry. This success underscores the versatility and adaptability of Malaysia’s diecasting sector in meeting the diverse needs of high-tech industries and contributing to the country’s economic development.
Looking forward, the prospects for Malaysia’s diecasting industry appear bright. The global trend towards lightweight and fuel-efficient vehicles is expected to drive continued demand for diecast aluminum components in the automotive sector. Similarly, the ongoing expansion of the electronics industry will create new opportunities for diecasters. To capitalize on these trends, Malaysian diecasters must continue to invest in technological innovation and sustainability. Enhancing production efficiency and reducing environmental impact will be crucial for maintaining competitiveness. Continued government support for research and development, coupled with a favorable business environment, will be essential for sustaining the industry’s growth. By embracing these opportunities, Malaysia can further solidify its position as a leading player in the global diecasting market, driving industrial excellence and economic progress.
In conclusion, diecasting has become an integral part of Malaysia’s industrial fabric, fueling the growth of key sectors such as automotive and electronics. The evolution of the diecasting industry, propelled by technological advancements and strategic initiatives, has enabled Malaysia to compete effectively on the global stage. As the demand for high-quality diecast components continues to rise, the future of diecasting in Malaysia looks promising. By investing in innovation, maintaining high standards, and focusing on sustainability, Malaysian diecasters can seize new opportunities and contribute significantly to the country’s economic development. The journey of diecasting in Malaysia is a testament to the nation’s commitment to industrial excellence and technological progress, highlighting its role as a catalyst for industrial innovation and growth.